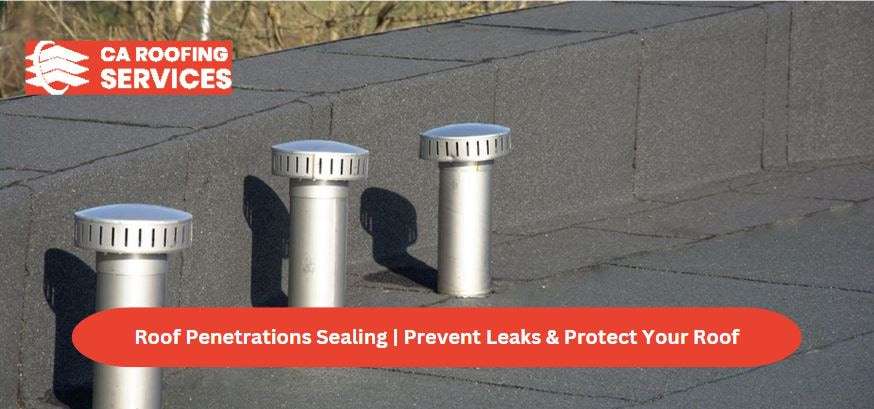
Roof Penetrations Sealing | Prevent Leaks & Protect Your Roof
Is your commercial roof truly protected from leaks? Roof penetrations, such as HVAC units, vent pipes, and skylights, are essential for building function but can become major weak points if not sealed properly. Even a small gap around a penetration can lead to costly water damage, mold growth, and structural issues.
Proper Roof penetrations sealing isn’t just a precaution—it’s a necessity to keep your building safe, dry, and secure. But what makes a seal truly effective? Let’s explore the best practices and strategies for keeping your roof watertight.
The Importance of Maintaining a Watertight Commercial Roof
An ideal commercial building should have a solid and also a watertight roofing system. Flood or water damage is expensive because it leads to things such as structural damage, formation of mold, and costly repair work. These or even worse circumstances can be avoided through having proper waterproofing on the roof to keep your property in a good state and fully operational.
Why is Proper Sealing So Important?
Water leakage is a common problem related to roofing and should be addressed before it becomes a major issue that may lead to further damage. When it comes to roofing, sealing ensures that the roof does not develop any issues related to water damage. When for instance penetrations which include A/C’s and vents are not properly sealed, it results in formations of avenues that let water in easily.
This can lead to:
- Costly repairs from water damage.
- Structural weakening over time.
- Mold growth, which can affect air quality.
- Disruption of daily business operations.
Sealing your roof properly ensures long-term durability and reduces maintenance costs.
Understanding Roof Penetrations
What Are Roof Penetrations?
Roof penetrations sealing are any openings or structures that break through the roof’s surface. These include:
- HVAC units – Essential for ventilation and climate control.
- Vent pipes – Used for plumbing ventilation.
- Chimneys – Often found in buildings with fireplaces or heating systems.
- Skylights – Add natural lighting but can be prone to leaks if not sealed well.
Why Are Roof Penetrations Vulnerable?
Since Roof penetrations sealing break through the roof’s protective barrier, they create weak spots where water can enter if not properly sealed. Over time, exposure to rain, wind, and fluctuating temperatures can weaken the seals, making leaks more likely.
Common Challenges with Roof Penetrations
Even with proper installation, Roof penetrations sealing can present challenges.
1. Leaks from Poor Installation or Maintenance
If the sealing materials or flashing are not installed correctly, leaks can develop quickly. Lack of regular inspections may also allow minor issues to become major problems.
2. Weather Damage
Extreme weather conditions, like heavy rain, strong winds, and temperature fluctuations, can wear down sealants over time. UV rays from the sun can also cause sealants to crack or dry out.
3. Multiple Penetrations Close Together
When HVAC units, vents, and other structures are positioned too closely, it becomes harder to apply proper sealing techniques. This overlap can increase the risk of leaks.
How Can You Prevent Roof Penetration Issues?
- Use High-Quality Sealants – Choose materials specifically designed for Commercial roof maintenance and weather resistance.
- Hire Professional Roofers – Ensure installations are done correctly with proper flashing techniques.
- Regular Inspections – Schedule routine maintenance to catch small issues early.
- Weatherproof Solutions – Use UV-resistant and weatherproof types of sealants for long-term sealing.
Preserving the watertight ability of your commercial roof is a worthy investment that prevents expensive repair jobs. When was the last time you went to inspect the condition of your roof?
Best Practices for Roof penetrations sealing
Roof penetrations sealing properly is key to keeping your commercial roof watertight and preventing costly water damage. But how can you ensure it’s done right? Here are some effective practices to follow:
1. Use the Right Flashing Techniques
Not all roof penetrations are the same, so they need different flashing methods. For example:
- HVAC units: Require metal flashing with flexible seals.
- Vent pipes: Need specialized boots or collars.
- Skylights: Work best with step flashing and waterproof membranes.
Flashing directs water away from the penetration, so using the correct technique ensures long-term protection.
2. Choose High-Quality Sealants
The sealant you pick makes a big difference! Always use sealants designed for roofing, such as:
- Silicone or polyurethane for their flexibility and weather resistance.
- UV-resistant sealants for long-term durability.
Cheap or incorrect sealants can crack and fail quickly, leading to leaks.
3. Follow Manufacturer Guidelines
Every roofing material and product has specific instructions for use. Ignoring these can lead to improper sealing and void warranties.
- Follow recommended thickness and drying times.
- Ensure compatibility between sealants and roofing materials.
4. Stick to Industry Standards
Professional roofers follow industry standards like those set by the NRCA (National Roofing Contractors Association). These standards ensure consistent, reliable sealing practices.
Sealing HVAC Roof Penetrations
HVAC units are common on commercial roofs, but they come with unique challenges. Why? They deal with vibration, heat, and movement, all of which can strain the seals. Here’s how to seal them properly:
1. Account for Vibration and Thermal Expansion
HVAC units vibrate during operation and expand with heat. This movement can break down seals over time if not addressed properly.
- Use flexible sealants that can expand and contract.
- Apply reinforced flashing to handle constant movement.
2. Ensure a Proper Seal Around the Entire Unit
Gaps around HVAC units are common leak points. Make sure to:
- Seal all edges, especially corners and seams.
- Apply a double layer of sealant where needed for extra protection.
3. Regular Maintenance is Key
Even the best seals wear out over time. Schedule regular roof inspections to:
- Check for cracks or worn-out sealants.
- Reseal areas showing early signs of damage.
A Watertight Roof is a Smart Investment
Properly sealed roof penetrations save you from expensive repairs, structural damage, and downtime. When was the last time you had your roof professionally inspected? Investing in quality sealing today can prevent major issues tomorrow.
Vent Waterproofing Strategies
Properly sealing vent pipes and ducts is essential for keeping your commercial roof watertight. Vents are common points of water entry, so sealing them the right way can save you from costly repairs.
How Can You Effectively Seal Vent Pipes and Ducts?
- Use Vent Boots: These specialized rubber or metal covers fit around the base of vent pipes to create a tight seal.
- Apply Waterproof Sealants: Use high-quality, weather-resistant sealants like silicone or polyurethane to seal around the vent edges.
- Install Flashing: Metal flashing around vent bases directs water away, preventing pooling and leaks.
Preventing Common Vent Issues
Vents can face problems beyond leaks. Here’s how to avoid them:
- Condensation Control: Insulate vent ducts properly to prevent moisture buildup inside the pipe.
- Backdraft Prevention: Ensure proper vent height and positioning to avoid wind-driven backdrafts pushing air back inside.
Regular Inspection and Maintenance
Sealing isn’t a one-time job. Regular roof maintenance is essential for keeping your roof in top condition.
How Often Should You Inspect Your Roof?
It’s recommended to inspect your roof at least twice a year, especially after extreme weather.
What to Look for During Inspections?
- Cracked or Peeling Sealants: Sealants can wear out over time, so check for cracks or gaps.
- Loose Flashing: Ensure flashing remains secure and free from rust or damage.
- Pooling Water: Standing water around penetrations indicates drainage issues that need fixing.
Steps for Maintaining Sealants and Flashings:
- Remove old, worn-out sealant before applying a new layer.
- Clean the area thoroughly to ensure the new sealant bonds well.
- Replace any damaged flashing promptly to prevent leaks.
Case Studies: Successful Roof penetrations sealing
Case 1: Waterproofing Vent Pipes on a Retail Store
A retail store in a high-rainfall area experienced frequent leaks around vent pipes. By installing vent boots and resealing with UV-resistant sealant, leaks were eliminated.
Lesson Learned: Regular inspections would have caught the failing seals earlier, preventing costly water damage.
Case 2: HVAC Penetration Sealing for a Commercial Office
An office building faced leaks due to vibration damage around HVAC units. The solution involved:
- Using flexible sealants designed for movement.
- Applying double layers of flashing for extra protection.
Lesson Learned: HVAC units require flexible materials to handle constant movement and heat expansion.
Conclusion
Are you confident your Roof penetrations sealing are sealed for long-term protection? Investing in quality sealing techniques, regular inspections, and durable materials can prevent expensive repairs and extend the life of your commercial roof. From vent pipes to HVAC units, every penetration matters when it comes to keeping water out. Don’t wait for a leak to remind you—when was the last time your roof was professionally inspected? Stay proactive and protect your investment with reliable roof penetration sealing solutions.
FAQs
- Why is sealing roof penetrations important?
Sealing roof penetrations prevents water leaks, structural damage, and mold growth by keeping moisture out of vulnerable areas. - What materials are best for sealing roof penetrations?
High-quality sealants like silicone, polyurethane, and EPDM, along with proper flashing, offer durable and weather-resistant protection. - How often should roof penetrations be inspected?
Roof penetrations should be inspected at least twice a year and after major weather events to ensure seals remain intact and effective.